UC Davis EPA P3 Biofertilizer Team
Tyler Barzee, Hossein Edalati, Tanner Garrett, Ashwin Bala
Professor Ruihong Zhang (PI)
The Vast Dairy Industry
California is the leading dairy producer in the US producing 30 million tons of manure annually that could meet the nutrient needs of the state’s commercial crop industry
Environmental Challenges with Manure and Nutrient Management
Anaerobic lagoons storing dairy manure cause substantial methane and other greenhouse gas emissions (GHG) while synthetic fertilizer production needs huge amounts of energy and produces 4% of total anthropogenic GHG emissions each year!
Manure is prone to be applied excessively in lands surrounding dairies and can lead to nutrient pollution
Research Need:
Anaerobic digestion can convert manure into renewable energy, reducing GHG emissions but the digestate needs to be further processed to create solid products that can be shipped off of farms economically for use in the state’s many specialty crop farms.
Sustainable Bio-Fertilizer from Anaerobically Digested Animal Manure

New Hope Dairy Digester in Galt, CA
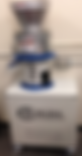




People
Reduce environmental impacts from synthetic fertilizer production
Encourage renewable and clean energy development in rural areas
Prosperity
Turn waste into profit
Create new, technical jobs in agricultural sector
Planet
Create sustainable nutrient cycle within the agriculture industry
Decrease GHG and nutrient pollution
Phase I Objectives:
•Research and demonstrate effective separation technologies for treatment of digestate to yield solids, nutrients, and water streams;
•Design and produce novel, nutrient-rich, cost-effective and safe biofertilizer products and to evaluate their effectiveness on vegetable production; and
•Conduct an economic analysis and environmental assessment for application in dairy manure digester systems and disseminate project results to dairy farmers and crop production consultants.



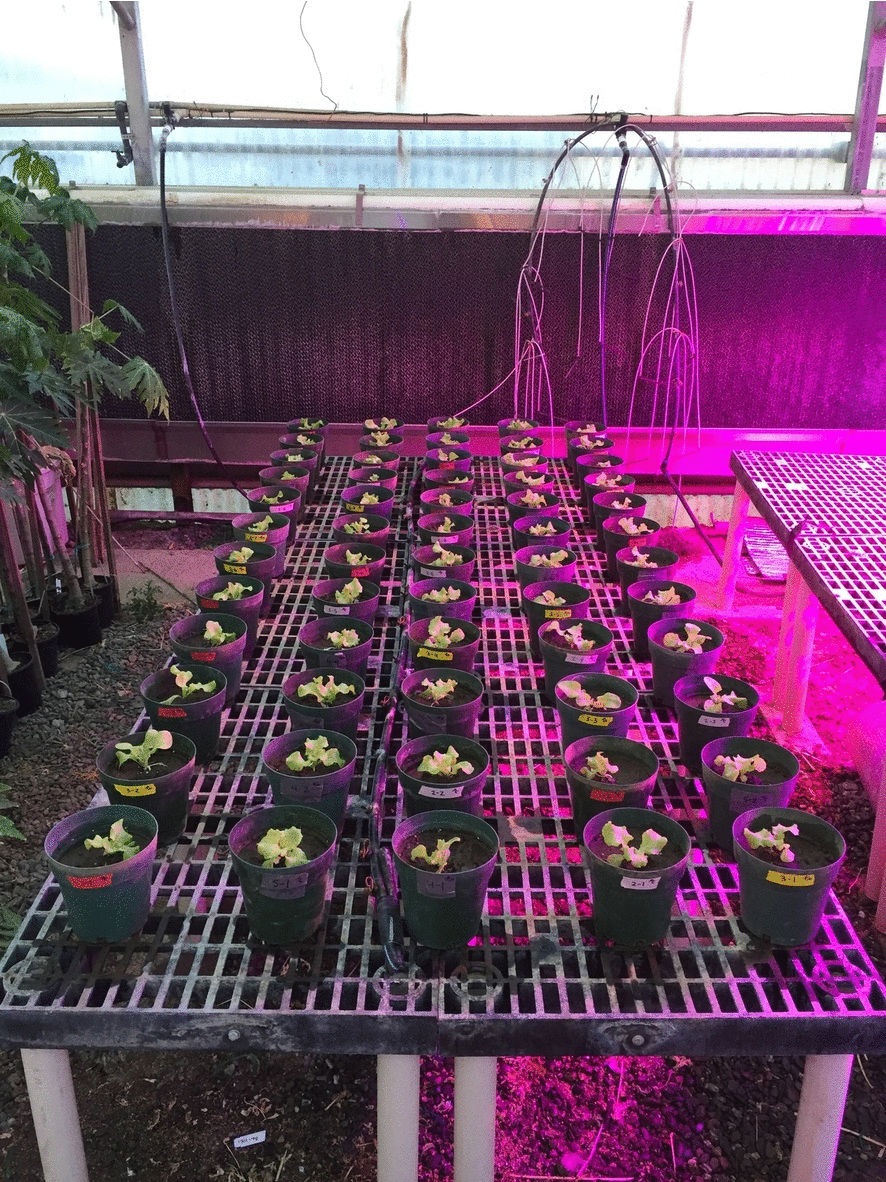



Lettuce Growth Trials with Pelletized Biofertilizers
Our small scale integrated system treated up to 300 gallons per day of digestate (fig 3, 4), producing solid and liquid fractions, and consisted of a vibratory screen (fig 4A) for coarse solid separation followed by a membrane filtration unit (fig 4B) for fine solid separation. Pellets (solid product) were made by ambient air drying and pelletization (fig 5A/B) of the concentrated solids liquid stream. The final solid product (table 1) was tested in a greenhouse study with Black Seeded Simpson lettuce variety (fig 5C) and compared against no fertilizer control, Nutra-Gel (12-13-9) synthetic fertilizer and food waste digestate pellets (fig 6). More work is needed on product formulations but early results are promising
The research team developed an economic model for an industrial scale digestate-biofertilizer production system. This model takes into account initial capital and operation and maintenance (O&M) costs as well as profits from the biofertilizer product revenue streams. The model shows high profitability and a Return on Investment (ROI) of less than 10 years for most scenarios.